Рубрикатор | ![]() |
![]() |
Статьи | ![]() |
![]() |
31 августа 2015 |
Нам нравятся нестандартные проекты
Компания Сabero, отмечающая в этом году 35-летие, в Россию пришла в 2011 г., гораздо позже большинства зарубежных поставщиков систем охлаждения. Однако за это время успела поучаствовать в нескольких масштабных проектах. О том, чего сегодня ожидает компания от российского рынка ЦОДов, – Александра ЭРЛИХ, генеральный директор Сabero.
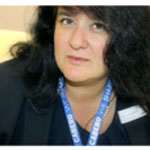
К о г д а к а ч е с т в о п о д к о н т р о л е м в л а д е л ь ц а
– Теплообменное оборудование производства Cabero, по оценкам российских проектировщиков, отличается идеальным соотношением цена/качество. Как удается его обеспечивать?
– Во-первых, за счет оптимального распределения персонала. У компании нет лишних служб. Даже маркетинг и ИТ мы передали на аутсорсинг, что позволяет задействовать эти службы только тогда, когда они действительно нужны. А во-вторых, Тино Каберо-младший, владелец компании и сын ее основателя, придерживается «принципа 150», согласно которому эффективно управлять можно предприятием именно с таким количеством сотрудников. Как только штат одного завода Cabero превышает 150 человек, открывается второй. По этой причине в Венгрии у нас два завода, которые изготавливают оборудование для Европы, включая Россию. Надо сказать, что этот принцип работает совсем неплохо: за счет гибкости и скорости реагирования мы часто выигрываем у крупных концернов, куда менее поворотливых, а кроме того, нам легче обеспечивать высокое качество нашей продукции.
Отдельно нужно отметить личный контроль за производством со стороны г-на Каберо. Среди прочих документов об образовании он имеет диплом сварщика, регулярно проходит аттестацию и периодически освежает на практике свои знания. Непосредственное участие в производстве дает ему возможность постоянно оптимизировать процессы.
– А чем отличаются агрегаты, которые выпускаются в России при участии Cabero?
– В России оборудование собирается и продается под брендом ProfITcool. Мы специально разделили наши торговые марки, чтобы у заказчиков, которым важно приобрести оборудование российской сборки, не возникало сомнений. При этом теплообменник в раме по-прежнему собирается в Германии, а в России проводится монтаж вентиляторов (тоже от проверенных немецких производителей) и электрики. Единственное отличие оборудования, которое собирают специалисты ProfITcool, – электрические шкафы, обеспечивающие работу в расширенном диапазоне температур, который отвечает российским условиям: от - 40 до + 40oC. Для нас важно, чтобы у заказчиков в вашей стране был выбор.
– В какие сроки окупается оборудования Cabero?
– Это зависит от страны и даже от региона, а точнее от того, какова стоимость электроэнергии. Другой немаловажный фактор – цена ремонта. Если в дешевых системах вам придется каждые три-четыре месяца что-то менять, то в случае с нашими агрегатами ценой ремонта можно пренебречь.
– А сколько лет они служат?
– Компания основана в 1980 г. Самому старому аппарату, о котором я знаю, сейчас 24 года. И это при том, что в Германии и вообще в Европе 15 лет – это срок амортизации, по истечении которого оборудование списывают. Откуда я узнала о самом старом аппарате? Он все это время исправно работал в Словакии, пока год назад не сломался вентилятор и заказчики не написали нам письмо с просьбой о его замене. Мы поставляем оборудование для разных сегментов рынка, в частности для охлаждения аварийных контуров атомных электростанций, в том числе российских. Так вот, Росатом на основе специальных расчетов подтвердил, что срок службы наших агрегатов – 60 лет.
– Но какое-то обслуживание этим машинам все-таки требуется?
– Тут все зависит от типа системы. Самый простой тип – сухой драйкулер. Он наименее энергоэффективен, требует наибольших инвестиций, но при этом прост в уходе. После установки его достаточно с определенной периодичностью мыть. Где-то это требуется делать раз в год, где-то раз в квартал. И все. Бывает, что в драйкулере выходит из строя вентилятор, но я ни разу не слышала, чтобы это произошло до истечения срока гарантийного обслуживания, а он у нас составляет пять лет. Гарантию мы совершенно спокойно продлеваем. Немногим большего ухода требуют наши системы орошения: нужно заниматься водоподготовкой, следить, чтобы не забивались форсунки, да и электрическая часть этих систем сложнее.
Э к с п е р т п о э н е р г о э ф ф е к т и в н о с т и
– Как оборудование компании Cabero – производителя компонентов – попадает в крупные проекты?
– Для нас это непросто, приходится тесно взаимодействовать с интеграторами, с проектировщиками. Так, наши авторизованные дистрибьюторы регулярно проходят обучение работе с нашей термодинамической программой. Она позволяет, задав небольшой объем данных, получить для проекта возможные варианты оборудования из более или менее стандартизованной линейки. Важно также, что практически с момента основания мы специализируемся на энергоэффективности. Знающие об этом заказчики часто привлекают нас в проекты как экспертов в этой области. Так мы оказались вовлечены в очень интересный проект – создание ЦОДа Академии Бундесвера в Штраусберге. Мы осуществляли его проектирование в части энергоэффективности систем охлаждения и регулирования. Вместо чиллеров в нем используются абсорбционные холодильные машины (винтовые чиллеры находятся в «холодном» резерве), а с абсорберами работает каскадная система, состоящая из наших гибридных машин и испарительных охладителей системы HPSS. Она обеспечивает ЦОДу 30%-ную экономию затрат на электроэнергию. Еще 10% получается за счет внедрения централизованной системы управления, разработанной нашим дочерним предприятием.
– А в России подобные проекты реализованы?
– Единственная полностью бесчиллерная система, построенная на оборудовании Cabero, в России используется для охлаждения новейшего суперкомпьютера в Научно-исследовательском вычислительном центре МГУ им. М.В. Ломоносова. В этом проекте дополнительно к нашим абсолютно сухим, без испарителей, драйкулерам используется внутренняя система водяного охлаждения серверов.
На конференции «ЦОД-2015» я планирую раскрыть подробности разработанной нами для одного проекта системы наружного охлаждения, которая позволила на 10 К понизить температуру конденсации на один чиллер, а следовательно, на порядок уменьшить размер этой машины и на несколько порядков – ее энергопотребление. Результаты и с инженерной, и с экономической точки зрения получились выдающимися.
– Получается, что будущее за бесчиллерными решениями систем охлаждения?
– Безусловно. В системе охлаждения чиллер – это основной потребитель не только инвестиций, но и электроэнергии. Это довольно сложная комплексная система, целый машинный зал в одном корпусе, который «ест» очень много. Существуют несколько вариантов бесчиллерных систем – от использования солнечных коллекторов в двух направлениях до погружных систем охлаждения для серверов в дата-центрах. И все они, с моей точки зрения, имеют право на жизнь.
С е к р е т ы «и н д п о ш и в а»
– Как специалистам Cabero удается обеспечить индивидуальный подход к каждому заказчику?
– Заказчик всегда знает, что и где ему нужно охладить, какой получить результат. А дальше подключаемся мы. К примеру, в ЦОДах Белоруссии я не буду советовать использовать испарительное охлаждение, на севере России не предложу работать на самоопорожняющихся системах, а в южных районах, напротив, буду на этом настаивать. И тут чем глубже мы погружены в проект, тем больше можем помочь. Рассказав нам о своих потребностях немного подробнее, вы получите от нас много полезной информации, вплоть до рекомендаций по выбору материалов. Ведь ЦОДу, расположенному в центре города, и дата-центру, находящемуся в лесной зоне, нужны разные системы охлаждения.
– Сколько времени обычно занимает разработка таких индивидуальных предложений?
– Этот процесс может длиться от двух-трех часов до недели. Все зависит от того, как быстро мы сможем собрать наших специалистов для мозгового штурма. Для того чтобы сесть и подумать над предложением, люди должны освободиться от текущих дел. Кроме того, на срок влияет необходимость задействовать в проекте нестандартное оборудование, к примеру вентиляторы для работы в морском климате или взрывозащищенные вентиляторы. Тут мы полностью зависим от наших поставщиков. А поскольку они немцы, у которых все происходит размеренно, то ждать, что предложение будет выработано за два-три часа, не стоит.
– Каковы в таком случае ваши сроки изготовления и поставки оборудования?
– От четырех до 12 недель. Самое напряженное время у нас – IV квартал, поскольку все хотят вывезти оборудование до Рождества. В Германии есть традиция – закончить все дела до Нового года. И хотя в это время наши заводы работают в четыре смены, с валом заказов они все равно не справляются. В результате сроки удлиняются. Так что мы всех партнеров предупреждаем: «Если сроки критичны, давайте сделаем ваше оборудование пораньше – в сентябре или хотя бы оформим предзаказ».
– Какой объем поставки оборудования Cabero в Россию вам интересен?
– Любой. В этом году в честь юбилея компании мы объявили конкурс на самый интересный проект. Критериями выбора победителя являются не столько его объем и маржинальность, сколько красота инженерного решения, его оригинальность. И вполне возможно, что победителем станет именно самый интересный с технической точки зрения объект, а не самый дорогой.
Нам нравятся проекты, в ходе которых мы сами чему-то учимся. Все наши ноу-хау – самоопорожняющиеся системы, системы испарения, система абсорбционного холода – возникли именно в результате интересных клиентских проектов. Как раз такие сильные проекты, основанные на альтернативном подходе, обеспечивающем высокую энергоэффективность, мы и хотели бы видеть в российских центрах обработки данных.