Рубрикатор | ![]() |
![]() |
Статьи | ![]() |
ИКС № 2 2019 | ![]() |
![]() |
Сергей СОЛОВЬЁВ  | 07 мая 2019 |
Цифровые двойники в промышленности: сегодня и завтра
Технология «цифровых двойников», способная повысить производительность промышленных предприятий, распространена пока преимущественно на Западе, но есть все основания полагать, что в ближайшие годы и в России таких проектов станет заметно больше.
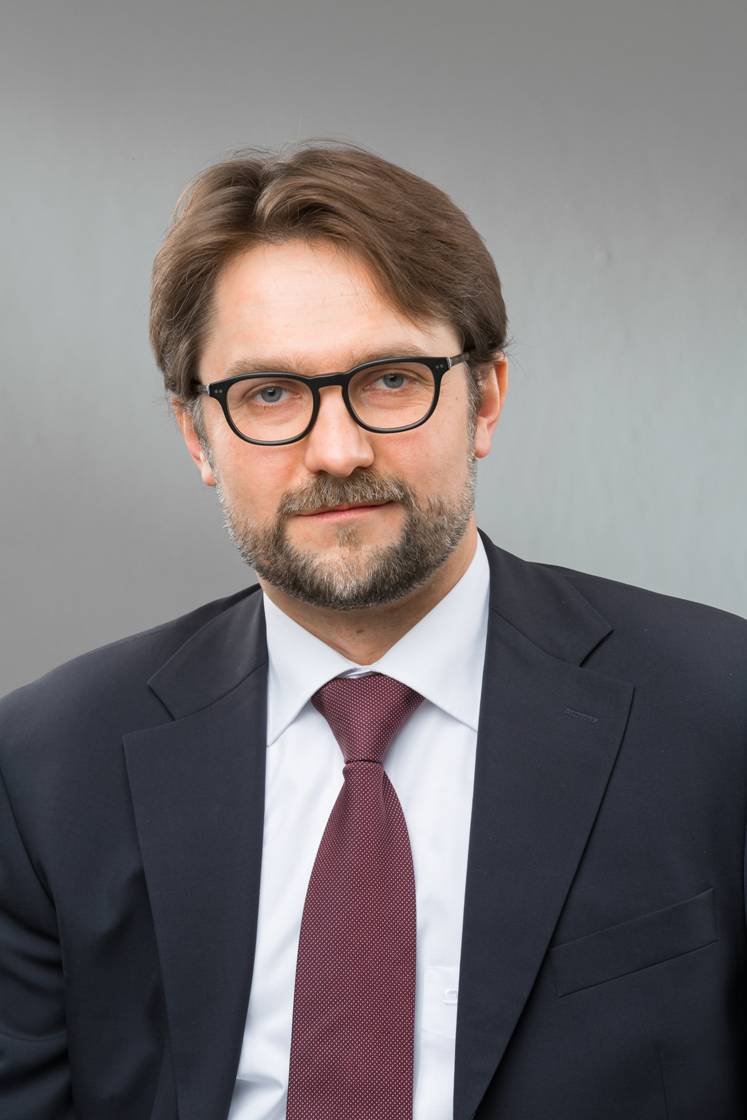
К 2021 г. половина всех крупных промышленных компаний, по прогнозу Gartner, будет использовать «цифровых двойников», и это повысит их производительность на 10%. Цифровой двойник – это виртуальная, имитационная модель чего-то физического, будь то люди, места, устройства, сложные системы, процессы или целые предприятия. Создание цифрового двойника позволяет смоделировать работу физического объекта еще на этапе его проектирования, более того, на протяжении всего жизненного цикла модель непрерывно генерирует данные о состоянии своего физического аналога в режиме реального времени.
Концепцию цифровых двойников (digital twins) впервые представил публике еще в 2002 г. профессор Мичиганского университета Майкл Гривз, выступая с презентацией, посвященной созданию центра управления жизненным циклом продукта (PLM). В частности, он говорил о возможностях, открывающихся при создании виртуального пространства, которое дублировало бы реальное пространство и обменивалось с ним потоками данных. Через год ученый опубликовал статью «Цифровые близнецы: превосходство в производстве на основе виртуального прототипа завода», после чего термин «цифровой двойник» прочно вошел в обиход. До недавних пор воплотить эту концепцию в жизнь было сложно и дорого, но стремительное развитие интернета вещей в корне изменило ситуацию, благодаря чему за последние пару лет цифровые двойники превратились в один из ведущих трендов технологического развития.
Чем цифровые двойники полезны промышленным компаниям
Технология может применяться в самых разных сферах, однако на сегодня наибольшее распространение она получила в промышленности – что неудивительно, поскольку цифровые двойники позволяют кардинально оптимизировать все процессы в производственно-сбытовой цепочке.
Обычно цифровой двойник продукта создается еще на этапе определения его концепции и проектирования. Это позволяет инженерам моделировать и оценивать особенности продукта в зависимости от установленных требований к нему, например, будет ли предлагаемая форма кузова обеспечивать минимально возможный коэффициент аэродинамического сопротивления или какова вероятность сбоев электроники в заданных условиях. С помощью цифрового двойника можно заранее протестировать и оптимизировать любые компоненты решения: механическую часть, электронные элементы, программное обеспечение, или производительность системы.
То же относится и к цифровому двойнику производства. Технология позволяет смоделировать в виртуальной среде практически что угодно, от станков и контроллеров до целых производственных линий, а также запустить предварительную оптимизацию производства, включая создание программ для программируемых логических контроллеров и виртуальную пусконаладку. Благодаря этому источники ошибок или сбоев можно выявить и устранить еще до начала реальной эксплуатации. При этом заметно экономится время и закладывается основа для индивидуализированного массового производства, поскольку даже самые сложные производственные маршруты можно быстро рассчитать, протестировать и запрограммировать с минимумом затрат и усилий.
Кроме того, продукты или производственные установки непрерывно передают данные о своей работе в цифровую модель производительности, благодаря чему ведется постоянный мониторинг состояния оборудования и показателей энергопотребления производственных систем. Это заметно упрощает процесс профилактического техобслуживания, предотвращает простои и уменьшает потребление электроэнергии.
Bausch + Ströbel планирует как минимум на 30%
повысить эффективность своих инженерных решений к 2020 г. На основе
цифровых данных разработчики и заказчик могут тестировать функции и
операторский интерфейс в центре виртуализации еще до сборки
оборудования. Цифровой двойник также позволяет провести виртуальный ввод
в эксплуатацию, выявляя дефекты, которые затем можно исправить, так что
реальный ввод в эксплуатацию происходит значительно быстрее. ![]() |
Отечественные первопроходцы
Если на Западе применение цифровых двойников уже становится стандартом в промышленности, то в России они пока не получили широкого распространения. Тем не менее ведущие компании страны в разных отраслях уже взяли на вооружение новую технологию.
В числе первых интерес к ней начал проявлять нефтегазовый сектор – в этой отрасли всегда внедрялись передовые технологии, а вдобавок ее стимулировали нынешние цены на нефть и растущая конкуренция со стороны альтернативных источников энергии. К примеру, «Газпром нефть» создала цифровые двойники установки гидроочистки бензина каталитического крекинга на Московском НПЗ и установки первичной переработки нефти на Омском НПЗ. Компания также работает над комплексными решениями в сфере цифровизации производства на базе заводов по производству битума в Рязани и в казахстанском Шымкенте.
Значимость технологии цифровых двойников осознают в энергетическом секторе: еще в 2017 г. «Росатом» объявил о планах создания цифровых АЭС, которые один в один будут повторять реальные станции. Это позволит не только собирать и эффективно применять данные о работе каждой отдельной единицы оборудования, но и создаст возможности для моделирования и прогнозирования работы объектов в различных условиях и режимах.
Курс на цифровизацию держит и сектор машиностроения. Так, в 2017 г. КамАЗ заключил партнерское соглашение с Siemens с целью перехода к цифровизации и внедрения в производственные процессы решений Индустрии 4.0. На данный момент в результате сотрудничества уже разработаны 3D-модели 20 универсальных станков, 28 станков с числовым программным управлением и нескольких десятков единиц оборудования, в том числе роботов, кантователей, манипуляторов, рольгангов и т.д. КамАЗ использует их для моделирования сборки, механообработки и других технологических процессов.
Технология создания виртуальных двойников также легла в основу проекта РЖД «Цифровая железная дорога», в рамках которого организована работа центра обработки и анализа данных, отвечающего за диагностику и сервисное обслуживание поездов «Ласточка» от «Уральских локомотивов».
Комплексный подход – долгосрочная конкурентоспособность
Пока большая часть примеров применения цифровых двойников, как в отечественной, так и в мировой практике, – это виртуальные модели отдельных элементов производства: продуктов, оборудования, систем, линий и процессов. Но можно ожидать, что в дальнейшем компании все чаще будут подходить к вопросу комплексно, используя технологию на всех этапах цепочки добавленной стоимости, от проектирования до сбора и анализа информации, которую готовые и введенные в эксплуатацию продукты генерируют в ходе своего жизненного цикла.
Объединение всего оборудования в сеть и создание канала связи с системами более высокого уровня – что как раз и подразумевает комплексный подход – позволяет централизованно управлять ресурсами и производственными данными. Соответственно, сокращаются затраты на закупки и эксплуатацию – данные по заказам в этом случае доступны на всех уровнях компании, и она может выработать оптимальную стратегию распределения заказов на разные производственные площадки внутри организации. Кроме того, наглядное представление запасов материалов, логистических процессов и доступности инструментов помогает быстро оценивать текущую ситуацию и эффективно координировать деятельность.
Ценность комплексного подхода в области управления качеством не менее велика. Прежде всего, благодаря усовершенствованным процедурам документирования производственных процедур и параметров производители могут точно знать, какой компонент в каких продуктах был установлен, какие у него функции и как именно выполнена установка, что позволяет им целенаправленно устранять потенциальные проблемы. А кроме того, информация, регулярно поступающая с IoT-датчиков уже проданных и используемых товаров, позволяет с высокой эффективностью корректировать и оптимизировать процессы.
В целом использование комплексной модели данных, которая содержит всю информацию о производстве на всех этапах жизненного цикла, уменьшает время выхода продукции на рынок, повышая при этом гибкость и эффективность работы предприятия. В итоге компании, применяющие такой подход, успешно адаптируются к изменчивости и многообразию глобальных рынков, добиваются роста производительности и начинают более эффективно использовать электроэнергию и ресурсы, что обеспечивает им долгосрочную конкурентоспособность.
Хотя на первый взгляд переход к комплексному подходу кажется слишком сложным, уже сегодня существуют технологические решения, позволяющие максимально упростить и оптимизировать этот процесс. Все чаще предприятия, нацеленные на полный переход к цифровому производству, делают выбор в пользу открытых облачных операционных систем для интернета вещей, таких как MindSphere, поскольку подобные платформы позволяют в кратчайшие сроки разрабатывать промышленные IoT-решения, подключать самый широкий диапазон устройств, физических объектов и корпоративных систем, а также предоставляют доступ к мощным отраслевым приложениям для использования цифровых двойников и глобальной экосистеме партнеров-разработчиков.
Компания
Electra Meccanica из Ванкувера спроектировала и выпустила новый
трехколесный электромобиль SOLO с одним пассажиром за два года с
небольшой командой молодых инженеров, используя программное обеспечение
Siemens NX и Simcenter.![]() Источник: Electra Meccanica, Siemens AG |
Чего ожидать в ближайшие годы
Наряду с внедрением комплексного подхода к созданию цифровых двойников еще один значимый тренд в этой сфере – стремление технологических компаний научить виртуальную модель производства не только в мельчайших деталях отражать физический аналог, но и «думать», а также действовать автономно. Именно поэтому развитие возможностей искусственного интеллекта так актуально для цифровизации производства, и в ближайшие годы работа в этом направлении будет идти очень активно.
Что касается перспектив технологии цифровых двойников в России, то можно ожидать, что отечественные тренды будут развиваться в колее общемировых. Конечно, пока многие отечественные предприятия заметно отстают от западных, ведь в стране до сих пор немало фабрик и заводов, где десятками лет используется одно и то же оборудование. Безусловно, их модернизация потребует не только значительных инвестиций, но и изменения менталитета как руководства, так и сотрудников. Но компании-лидеры в разных секторах российской экономики уже активно используют эту перспективную технологию и тем самым задают вектор развития остальным игрокам, а стоимость технологических решений в данной сфере, равно как и стоимость IoT-устройств, неуклонно снижается, что в совокупности дает весьма позитивный прогноз.
Заметили неточность или опечатку в тексте? Выделите её мышкой и нажмите: Ctrl + Enter. Спасибо!